The Effects of Mixed Lubricants in Equipment
You might always have wondered what is exactly the effect of different lubricants mixed together in a machine, for instance, hydraulic oil mixed with gear oil or oil mixed with grease? Today this article will solve your puzzle of it.
The Effect Resulted by Mixed Lubricants
A direct effect on viscosity of oil
Mixing lubricants of the same type but with different viscosity obviously has a serious impact on the viscosity of lubricants within the asset. The final viscosity will be variable and based on the viscosity of the mixed fluid and the amount of mixing.
The viscosity of the lubricant is selected based on a specific film thickness. The film provides separation between the rolling element and the stationary element in the bearing. Factors affecting the thickness of this film are rotation speed, load on the shaft and viscosity of the fluid.
If the final viscosity of the mixed fluid is too low, the resulting oil film thickness will not be sufficient to provide sufficient separation of the two bearing elements, which may lead to failure. If the viscosity is too high, it will lead to increased energy consumption and increased heating. Imagine running in the water at the beach. The viscosity of water is 1. As the viscosity increases, more effort is required to flow through the water.
A serious effect on safety through pressure
Different types of lubricants have specific characteristics to meet the requirements of specific types of machines. For example, gear oil may contain thiophosphorus extreme pressure (EP) additives. This applies to almost all types of gears except worm gear configurations. Usually, the large gear in the worm gear configuration is made of brass or bronze material.
The PSIP additive is too corrosive and due to the long contact time between the large gear and the worm gear teeth, the heat and pressure generated is sufficient to activate the PSIP additive and cause it to erode the softer yellow metal bull gear. The result is corrosion, rather than malleable metal soaps that provide additional EP protection.
In many cases, hydraulic fluids contain anti-wear (AW) additives rather than EP additives. These AW additives are not chemically corrosive and therefore do not provide the same level of protection as EP additives. Another problem is that the viscosity of hydraulic oil is usually much lower than that of gear oil.
To comprehensive what happens when oil and grease mix, you must know well about the manufacturing process of grease. A thickening agent for grease is first made and then added to achieve the desired grade. So the ratio of base oil can be easily changed to thicker, and resulted in a worse consistency grade. With the problem of viscosity and incompatibilities, you will find a recipe for disaster when mixing lubricants.
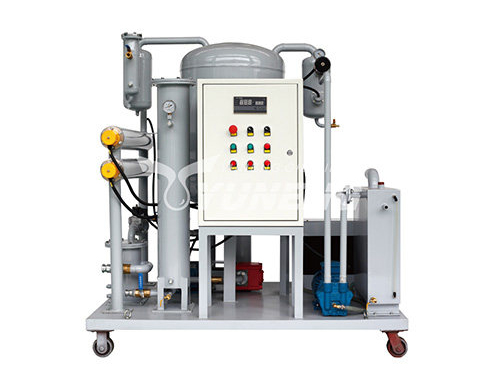
How to Avoid The Effect of Mixed Lubricants?
A lube oil blending machine can be applied to make different kinds of lubricants, for instance, transformer oil, hydraulic oil, heat transfer oil, etc. According to the required product, various base oils are added to the mixing vessel at a fixed ratio through flow indicators and controllers. Then dehydration under atmospheric pressure, adding various additives, through full mixing and heating, finally get the desired oil. It can separate different kinds of lubricants very well.
Advantages of Lube oil blending machine.
- The heating temperature of the oil could be set by the control cabinet on the machine
- With constant temperature heating system to ensure heating more uniformly and avoid damaging the oil quality
- Full automatic control
- Energy saving
- Easy to control and low labor cost
If you are still being bothered by lube oil mixing issues, you’d better use a lube oil blending machine, it can solve much trouble during work, China Oil Purifier is one of the most professional oil purifier manufacturers in China, if you are looking for oil issues assistance, please do contact us for help.